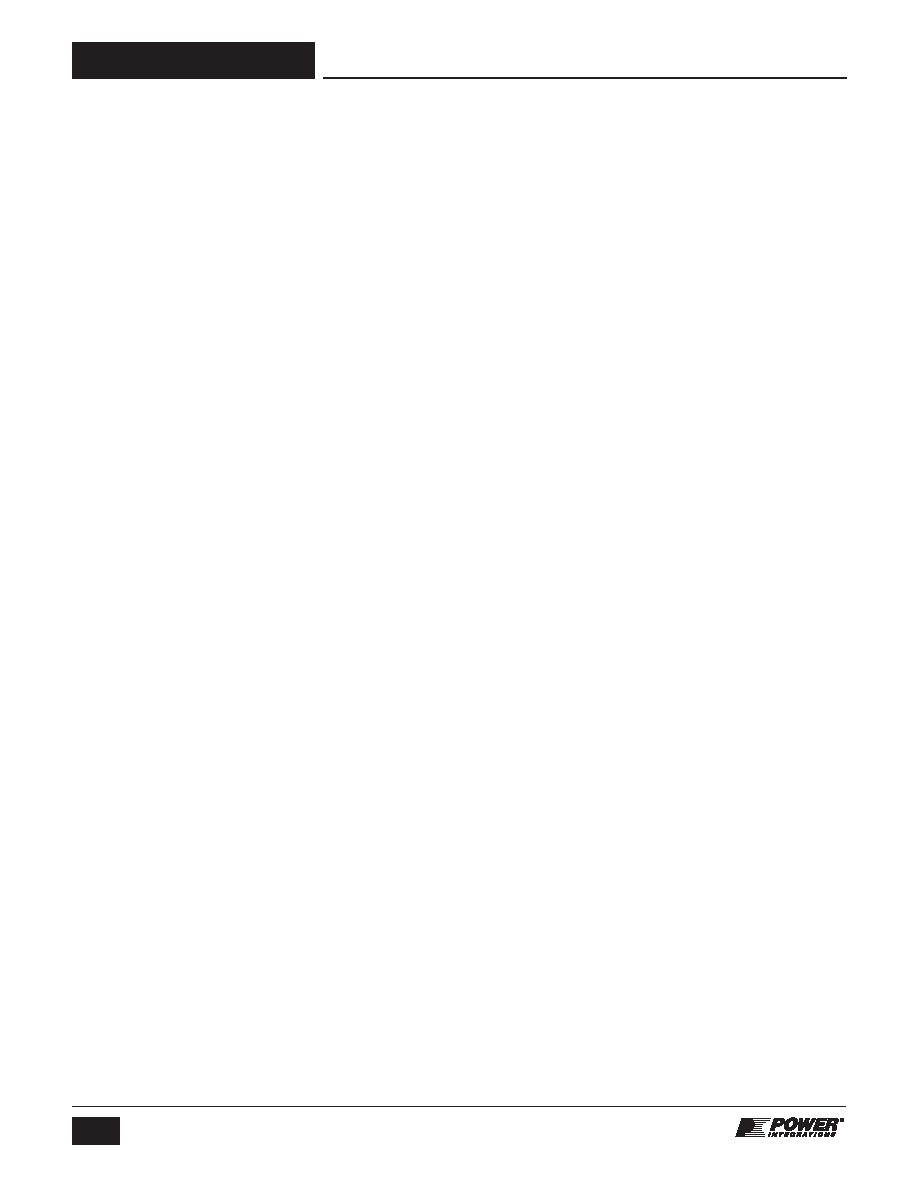
Rev. A 11/09/10
12
PFS704-729EG
www.powerint.com
Design, Assembly, and Layout Considerations
Power Table
The data sheet power table as shown in Table 2 represents the
maximum practical continuous output power based on the
following conditions:
For the universal input devices (PFS704-716):
1. An input voltage range of 90 VAC to 264 VAC
2. Overall efficiency of at least 93% at the lowest operating
voltage
3. Use of ultrafast recovery diode or high performance diode for
PFC output.
4. Sufficient heat sinking to keep device temperature ≤100 C
5. 380 V to 385 V nominal output
For the 230 V only devices (PFS723-729):
1. An input voltage range of 180 VAC to 264 VAC
2. Overall efficiency of at least 96% at the lowest operating
voltage
3. Use of ultrafast recovery diode or high performance diode
for PFC output.
4. Sufficient heat sinking to keep device temperature ≤100 C
5. 380 V to 385 V nominal output
Operation beyond the limits stated above will require derating.
Use of a nominal output voltage higher than 390 V is not
recommended for HiperPFS based designs. Operation at
voltages higher than 390 V can result in higher than expected
drain-source voltage during line and load transients.
HiperPFS Selection
Selection of the optimum HiperPFS part depends on required
maximum output power, PFC efficiency and overall system
efficiency (when used with a second stage DC-DC converter),
heat sinking constraints, system requirements and cost goals.
The HiperPFS part used in a design can be easily replaced with
the next higher or lower part in the power table to optimize
performance, improve efficiency or for applications where there
are thermal design constraints. Minor adjustments to the
inductance value and EMI filter components may be necessary
in some designs when the next higher or the next lower
HiperPFS part is used in an existing design for performance
optimization.
Every HiperPFS family part has an optimal load level where it
offers the most value. Operating frequency of a part will change
depending on load level. Change of frequency will result in
change in peak to peak current ripple in the inductance used.
Change in current ripple will affect input PF and total harmonic
distortion of input current.
Input Fuse and Protection Circuit
The input fuse should be rated for a continuous current above
the input current at which the PFC turns-off due to input under
voltage. This voltage is referred to as the brown-out voltage.
The fuse should also have sufficient I2t rating in order to avoid
nuisance failures during start-up. At start a large current is
drawn from the input as the output capacitor charges to the
peak of the applied voltage. The charging current is only limited
by any inrush limiting thermistors, impedance of the EMI filter
inductors and the forward resistance of the input rectifier
diodes.
A MOV will typically be required to protect the PFC from line
surges. Selection of the MOV rating will depend on the energy
level (EN1000-4-5 Class level) to which the PFC is required to
withstand.
Input EMI Filter
The variable switching frequency of the HiperPFS effectively
modulates the switching frequency and reduces conducted EMI
peaks associated with the harmonics of the fundamental
switching frequency. This is particularly beneficial for the
average detection mode used in EMI measurements.
The PFC is a switching converter and will need an EMI filter at
the input in order to meet the requirements of most safety
agency standards for conducted and radiated EMI. Typically a
common mode filter with X capacitors connected across the
line will provide the required attenuation of high frequency
components of input current to an acceptable level. The
leakage reactance of the common mode filter inductor and the
X capacitors form a low pass filter. In some designs, additional
differential filter inductors may have to be used to supplement
the differential inductance of the common mode choke.
A filter capacitor with low ESR and high ripple current capability
should be connected at the output of the input bridge rectifier.
This capacitor reduces the generation of the switching
frequency components of the input current ripple and simplifies
EMI filter design. Typically, 0.33
mF per 100 W should be used
for universal input designs and 0.15
mF per 100 W of output
power should be used for 230 VAC only designs.
It is often possible to use a higher value of capacitance after the
bridge rectifier and reduce the X capacitance in the EMI filter.
Regulatory requirements require use of a discharge resistor to
be connected across the input (X) capacitance on the AC side
of the bridge rectifier. This is to ensure that residual charge is
dissipated after the input voltage is removed when the
capacitance is higher than 0.1
mF. Use of CAPZero integrated
circuits from Power Integrations, helps eliminate the steady
state losses associated with the use of discharge resistors
connected permanently across the X capacitors.
Inductor Design
It is recommended that the inductor be designed with the
maximum operating flux density less than 0.3 T and a peak flux
density less than 0.42 T at maximum current limit when a ferrite
core is used. If a core made from Sendust or MPP is used, the
flux density should not exceed 1 T. A powder core inductor will
have a significant drop in inductance when the flux density
approaches 1 T.
When operated at the lower end of the input voltage range, the
value of K
P (the ratio of peak to ripple current) of the drain
current at the peak of the input voltage waveform should be